Current Location: yxcbearing >> Products >> Spherical Roller Bearing >> CC Series - Spherical Roller Bearing - 3Y Bearing
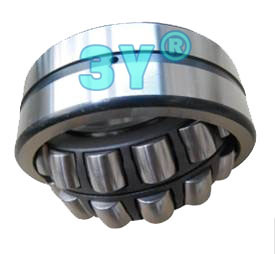
CC Series - Spherical Roller Bearing - 3Y Bearing
CC Series - Spherical Roller Bearing
Spherical roller bearings, with two rows of rollers, mainly bear radial load, but also can withstand the axial load in either direction. They have high capacity of radial load, especially suitable for work in heavy load or vibration load, but cannot bear pure axial load. The raceway in outer ring of this kind of bearing is spherical shape, so its alignment performance is good, which can compensate for coaxiality error. There are two symmetrical spherical roller, the outer ring has a common spherical raceway, the inner ring has two raceways that have certain angle with the bearing axis tilt, with good self-aligning performance. When the shaft is bent or installed different body bearing can still be used normally; self-aligning performance depends on different series of bearing size, the general allowed self-aligning angle of 1-2.5 degrees. Bearings with this type is large in load capacity: in addition to the radial load, the bearing can also withstand the two-way axial load, having a good impact resistance. Generally speaking, the Spherical roller bearing are allowed to work at a lower speed.
Spherical roller bearings are divided into symmetrical spherical roller and asymmetrical spherical roller according to the shape of the roller cross-section, with asymmetrical spherical roller bearings early products, mainly servicing for the mainframe maintenance. The newly design of the mainframe is rarely used symmetrical spherical roller bearings, which internal structure can withstand greater axial load, compared with the early produced of Spherical roller bearing, after comprehensive improvement and optimization in parameter. The operating temperature of this bearing is lower, so it can adapt to the requirements of higher speed. According to the inner ring with or without baffle and the different cage used, this type of bearing can be divided into type C and type CA, type C is characterized by the inner ring without baffle and the use of steel plate stamping cage, type CA Terrain bearing is characterized by the inner ring on both sides of the baffle and the use of car solid cage. In order to improve the lubrication of the bearings, we can provide the Spherical roller bearing with annular oil groove and three oil holes in the outer ring, which are indicated by the rear code: /W33. In line with the requirements of customers, we can also supply with Spherical roller bearing with oil hole in inner ring. For easy loading and replacing, we can also provide the Spherical roller bearing with a taper in inner hole, with a taper of 1:12, which is indicated by the rear code: K. And to meet the requirements of special users, we also provide bearings with inner hole taper of 1:30, indicated by the rear code: K30. Bearings with taper in inner hole can be installed onto the tapered journal by the locking nut or mounted on the cylindrical journal with the help of adapter sleeve or withdrawal sleeve. In order to prevent some harmful slip between the raceway and roller caused by the centrifugal effect in high-speed operation, the bearing should bear a certain minimum radial load, the size can be estimated according to the following formula:
Fr = 0.02C
where
Fr – minimum radial load N
C – basic rated dynamic load of bearing N
the equivalent dynamic load
P = Fr + Y1Fa, when Fa/Fr e,
P = 0.67Fr + Y2Fa, when Fa/Fr e,
where
P – equivalent dynamic load N
Y1 Y2 – axial dynamic load factor
Equivalent static load
P0 = Fr + Y0Fa
where
P – equivalent static load N
Y0 – axial static load factor
Type of Structure
Spherical roller bearing are divided into cylindrical bore and tapered bore.
The taper of the tapered bore is 1:12, with rear code K for Spherical roller bearing (type 153000 or 113000) and 1:30 rear code K30 for Spherical roller bearing. When such bearings are paired with tapered shaft, the inner circle can adjust the bearing radial clearance moving along the axial direction.
Rear Code
Type 153000 or 113000
Application
Mainly applicable cages: stamped steel plate reinforced cage (suffix E), stamped steel plate type of cage (suffix CC), glass fiber reinforced polyamide 66 cage (suffix TVPB), machined brass two-piece cage (suffix MB), machined brass integral type of cage (suffix CA), stamped steel plate cage for vibration occasion (suffix JPA) and brass cage for vibration occasion (suffix EMA). The bearing with same structure may be different in the code.
Main applications: paper making machinery, reduction devices, railroad vehicle axles, rolling mill gear box bearing housings, rolling mill rollers, crushers, vibrating screens, printing machinery, woodworking machinery, various industrial reducers and vertical spherical bearings with seats.
Installation
Spherical roller bearing assemble with drum roller bearings between the inner ring with two raceways and the outer ring with raceway of spherical surface. The curvature center of the outer ring raceway surface is same as the center of the bearing, so it has the same self-aligning function as the self-aligning ball bearing. In case of deflection of shaft and housing, it can automatically adjust the load and axial load in two directions. Radial load capacity is large which is suitable for situations with heavy load and impact load. Bearings with tapered inner ring bore can be mounted directly. Or it can be mounted on cylindrical shaft by using adapter sleeve and dismantling cylinder. The cage uses steel plate stamping cage, polyamide forming cage and copper alloy turning cage.
For self-aligning bearings, the use of an intermediate mounting ring will prevent the outer ring from tilting and rotating when fitting the bearing with the shaft into the box. It should be remembered that some sizes of self-aligning ball bearings have balls protruding from the side of the bearing, so the intermediate mounting ring should be recessed to prevent damage to the balls. A large number of bearings are generally mounted using mechanical or hydraulic press-in methods.
For separable bearings, the inner ring and outer ring can be installed separately, which simplifies the installation process, especially when the inner and outer rings are required for interference fit. When installing the bearing with the inner ring which has been installed into bearing box with the outer ring which has been included in, it must be paid attention to see whether the inner and outer ring is correctly aligned to avoid scratching the bearing raceway and rolling parts. If cylindrical and needle roller bearings use inner rings without flange retaining edge or with flange edge on one side, it is recommended to use mounting sleeves. The outer diameter of the sleeve should be equal to diameter F of the inner ring raceway and the tolerance standard for machining should be d10. It’s best to mount the drawn cup needle roller bearings using an arbor.
Clearance
For the axial clearance in the installation of self-aligning roller bearing, the nut for adjustment on the journal is available for adjusting the shim and the thread in bearing seat hole, or with preload spring and other methods to adjust. The size of the axial clearance is related to bearing installation arrangement, bearing distance, shaft and bearing seat material, and can be determined according to the working conditions. For self-aligning roller bearing with high load high speed, to adjust the clearance must consider the temperature rise on the axial clearance, and the the clearance reduction caused by temperature rise is estimated, that is to say, the axial clearance to be properly adjusted to larger. For bearings in low speed and bearing vibration, it should take no clearance installation, or apply preload installation. The purpose is to produce good contact between the roller and raceway of the self-aligning roller bearing with an uniform distribution of load, to prevent the roller and raceway was destroyed by the vibration impact. After adjustment, the size of the axial clearance is tested by a micrometer. The method is to firstly fix the micrometer in the body or bearing seat, so that the contact of the micrometer can hold against the clean surface of the shaft, along the axial to left and right, and the maximum swing of the needle is the axial clearance value.
Notes:
The preload of self-aligning roller bearing is carried out at room temperature, but in working condition, the drive shaft generated by system micro-tensioning temperature rise, which will make the bearing preload change, therefore, the setting of the preload should take into account this factor.
It needs the capacity of the size, speed, and other conditions set to make good use of the preload of self-aligning roller bearing to ensure the life of the transmission. If the preload is too large, it will cause power consumption, and even lead to overheating. If the preload is too small, then it comes with the body load, shaft rolling, and producing runout, run, transmission accuracy under the influence of the difference among the outer ring, to reduce noise increases, affecting the gear mesh and even serious damage when the teeth and bearings.
According to different assembly of self-aligning roller bearing, such as: directly rotate from the axial to the bearing preload nut of compressed inner bearing in its inner ring, with inner and outer ring to eliminate the gap and then to achieve the purpose of bearing preload force. To achieve common use: first, far more than the preassembled bearing in the last part of the nut, and then back by 1/4 turns. As for the assembly method, the advantages of this method is less investment, simple, practical and common tapered roller bearings given the excellent quality, it can all be used.
1. Electric heating method: Take the bearing placed on heating plate in the temperature of 100℃ electric for a few minutes. This method is the simplest one, if flipped several times, it can make the bearing evenly heated, and also high efficiency, and all Spherical roller bearing of different sizes can also use this method.
2. Electric furnace heating method: The bearings are heated in a closed automatic temperature-controlled electric furnace, which has uniform heating, accurate temperature control and fast heating, and is suitable for heating many bearings in one batch.
3. Induction heating method: using induction heaters can be fast, reliable and clean to heat Spherical roller bearing to required temperature, which is particularly suitable for bearings with tight inner ring. Because only the inner ring is heated and the outer ring heated very little, so it can be easier to install on the shaft, but also easy to install into the seat hole.
4. Electric bulb heating method: using 50W electric light bulb to heat the Spherical roller bearing, ensuring that the heating temperature at about 100℃. Smaller bearings can be placed directly on the bulb and larger bearings can be placed in the conical cover of bulb. Conical cover can prevent the heat loss, and produce uniform heat. Conical cover can be adjusted up and down, and can adapt to heating different sizes of bearings within a certain range. If the far infrared bulb, note that the direction of the bulb should be down, so as not to harm the human eye from infrared rays. This bulb is energy-saving. The bulb heating method is applicable to a small number and infrequent need. The bulb can also be used for lighting at other times, not needing any other equipment.
5. Oil tank heating method: This is a widely used traditional heating method. Set a metal mesh at the point of 50 – 70 mm from oil tank to the bottom, with bearings placed on the network and the large bearings to be lifted with a hook bearing and should not be placed directly in the bottom of the tank, to prevent too high heat of the part that contacts with the bottom of the tank, or the sediment dirt enters into the bearing. The oil tank heating method should be noted as the following: It should use mineral oil with non-corrosive and good thermal stability, preferably the transformer oil. The oil and container should be kept clean and the capacity of oil tank should depend on the size of the Spherical roller bearing heated and oil volume; if the container is too small, once a bearing is put into it, the oil temperature will drop quickly, resulting in a bad effect in continuous operation.